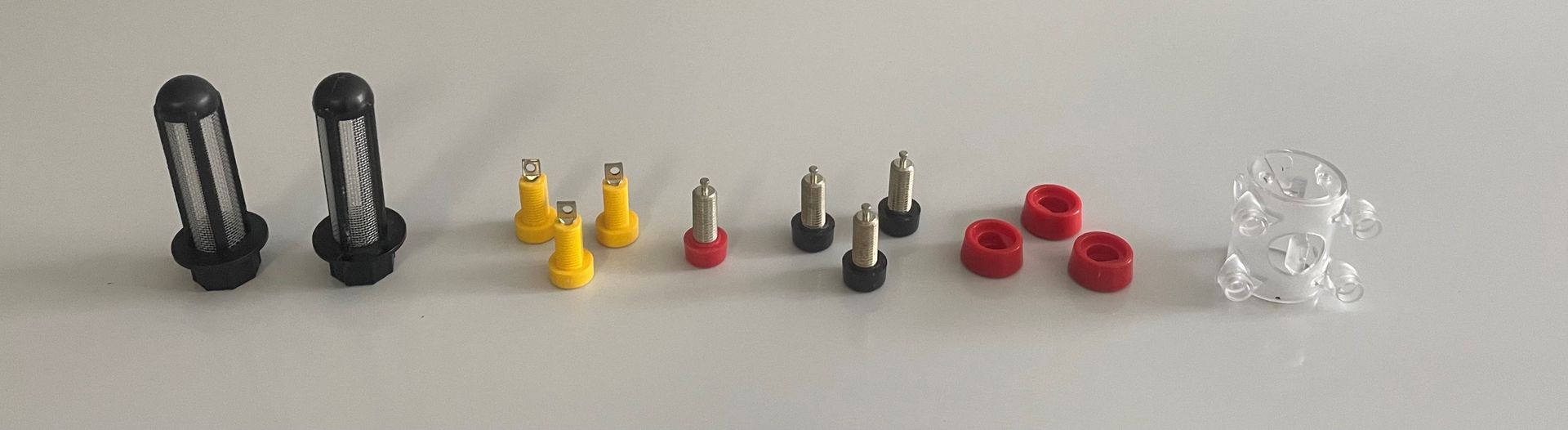
Our Process
We partner with your team throughout the project lifecycle to understand your unique needs and to design, manufacture, and assemble parts that meet your requirements.
Customized Project Management
Our team of engineers, project managers, and technicians are expert problem-solvers who deploy innovative plastic technology and thinking to meet your needs. Whether you require short, medium, or long production runs, or whether your parts require small or large tonnage presses, we have the equipment and expertise to deliver for you.
The EnTech Plastics Process
1
Engineering Design
Through our long-standing engineering-driven partnerships we’ll assist you in designing parts that meet your particular needs.
2
Fabrication
Once the design is approved, we can fabricate prototype parts that can then undergo your rigorous testing and evaluation requirements.
3
Tool Design & Build
Upon final part design, we develop and build your mold using tool steels appropriate for the application.
4
Production Part Approval
We undertake the Production Part Approval Process (PPAP) to ensure your complete satisfaction with the part.
5
Manufacturing
We produce the run to meet your specified and individualized needs.
High Quality Services, High Quality Products
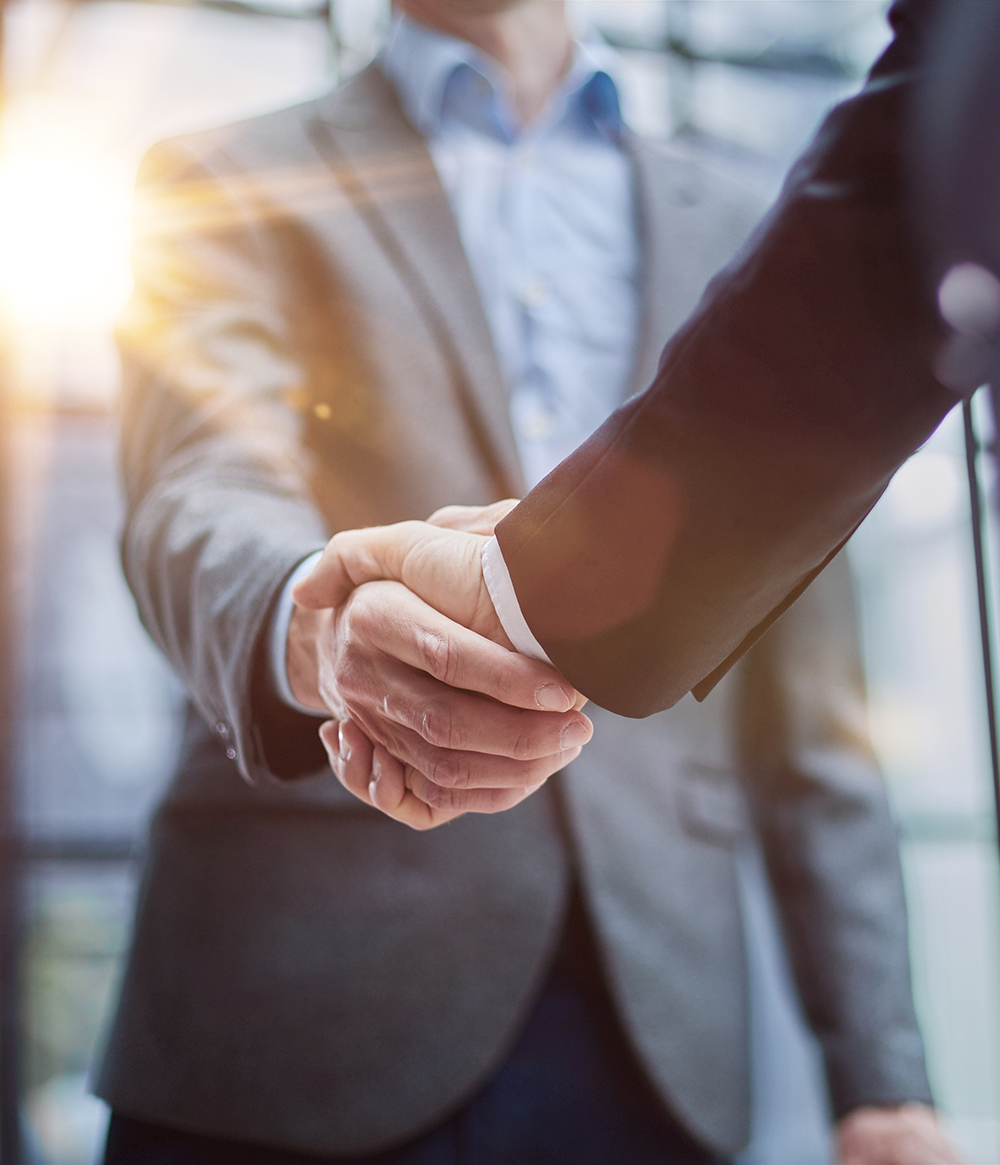
Count on EnTech Plastics for excellence both in parts and partnerships. Since 1996, we’ve forged strong relationships with customers, partners, and vendors to produce high quality parts with a focus on the processes and certifications that ensure consistency and continuous improvement.
To deliver consistent excellence, we utilize:
- Advance Quality Planning
- Production Part Approval Process (PPAP)
- Process validation including IQ, OQ, PQ
- Individual Quality plans customized to each job
- Statistical Process Control (SPC)
- In-House First Article Inspections (FAI), in-process inspections, final inspections
- Machine-side quality measurements tracked in our ERP system
- Calibrated surface plates, gram scales, gauge blocks, gauge pins, digital calipers, melt flow testing
- Customized inspection and test equipment where necessary
- Dedication to Continuous Improvement
- Off-site employee training in areas such as:
- Blue Print Reading
- Injection Mold Process Troubleshooting
- LEAN manufacturing
- Six Sigma
- Leadership Development
- Supervisory Leadership Skills
- Geometric Tolerancing
Sustainability Practices
We seek to employ cost-effective sustainability solutions throughout the planning, prototyping, and manufacturing phases of each project. Whenever possible, we promote the use of reprocessed resins. Reprocessed resins are an effective way to cut waste and improve cost competitiveness while at the same time ensuring a high-quality product. Over the years we have molded millions of pounds of reprocessed post-industrial plastic resins.
Where appropriate, we can help you meet your sustainability goals with natural fiber-filled materials or with biopolymers—100% biodegradable resins derived from 100% renewable resources. In the appropriate applications, biopolymers can replace traditional oil-based resins such as ABS, HIPS, and PP. Talk to us about your sustainability targets and we'll help you reach them.