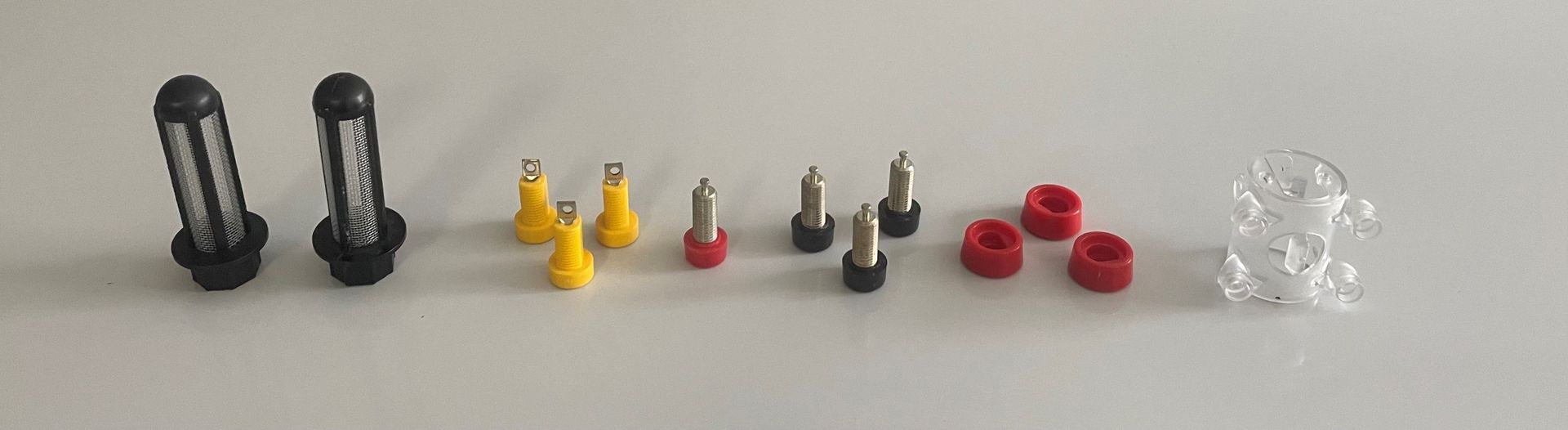
Services Offered
EnTech Plastics is a full-service injection molding manufacturer that merges two core competencies—Engineering and Technology. We’ll analyze your product concept and help to optimize your design for injection molding. Then we’ll design and build your tool, and finally we’ll bring your component into production in our modern injection molding facility.
Low Volume / High Tonnage Custom Injection Molding
Shorten run lengths, lead times and cut costs. By focusing on minimizing set up and start up times, we offer cost-effective low volume production runs, particularly in high tonnage machines. In many of our low volume programs we produce large plastic parts (weighing up to 22 pounds) in large tonnage injection molding machines (up to 1,100 tons) in run lengths of fewer than 1,000 parts per year.
With our state-of-the-art custom injection molding machines and decades of experience, we can ensure your project’s success using:
- DFM Services
- Gas-assist technology
- Insert molding technology
- Over molding technology
- Master Unit Die (MUD) Frames
- Engineering and general-purpose resins
- New product introductions and tool transfers
- Reshoring plastic parts
Gas Assist Injection Molding
Get higher quality components and lower costs with gas assist injection molding. We inject nitrogen gas into the hot melt stream during the molding process, displacing the resin in thick-walled sections, to create a hollow core. This innovative process is ideal for several important reasons:
- Increase Design Options: Since this process is not constrained by typical tool design requirements, parts with complex designs can be produced with less complicated tooling.
- Improve Part Quality: The Gas Assist process creates uniform pressure throughout the part which minimizes any potential warp issues. The technology can also be used to eliminate sink marks at rib and boss locations. Parts with varying wall thicknesses can be molded without the need for complicated cores.
- Reduces Costs: Since Gas Assist parts require less material and run at faster cycle times the corresponding piece prices are reduced accordingly.
- Part Consolidation: With gas assist molding, several components that would normally be produced separately with conventional injection molding can be combined into a single part.
Expert Engineering Services
Get to the heart of the part’s design. We go beyond simply ‘molding’ parts. Through our strategic partnerships with designers, tool shops and plastic technology providers we offer our customers critical services including:
- Design through Production Capability: An integrated approach to product development and manufacturing reduces project cycle time, optimizes part and mold design, minimizes manufacturing costs, and maximizes customer profits.
- Part Design:Whether you provide us with a “sketch on a napkin” or fully detailed part prints and files, we’ll ensure that your design is optimized for strength, stability, function, cost and longevity.
- Material Testing and Analysis: Since resin characteristics are key to the part’s function, we select the proper resin early in the development stage to help ensure the success of new product introductions.
- Plastic FEA (Finite Element Analysis): Used to evaluate stress, strain and other factors to solve part performance early and ensure a part’s future performance.
- Rapid Prototyping: Lets you evaluate new design concepts before incurring major tooling costs and reduces product development time and costs.
- Mold Flow Analysis: This injection molding process simulation and analysis program evaluates gate and runner designs and locations, cooling requirements, melt temperature and other processing variables, enabling the toolmaker to optimizes the tool design for manufacturability and part performance.
- Mold Design and Fabrication:
Our strategic alliances with local tool and die shops allow us to provide prototype and production mold fabrication services.
Tool Building Design Assistance
Our strategic tooling partners use CREO software to design tools that produce parts to your exact specifications. With deep experience across a number of industries, we’re able to manufacture high quality tooling optimized for specific market uses. We guarantee that the mold you contract with us to build will produce parts that meet your design specifications.
When designing a tool, we consider a variety of factors, including the number of shots, the specified resin, the projected mold life, and other critical factors. We then build the molds with steel tolerances of +/- 0.003″ or 0.075mm.
We offer the following tooling services.
- Full New Tool Program Management: Covers the complete tool development cycle from tooling concept through the finished manufacture and trial of the production tool.
- Satisfaction Guarantee: We guarantee that you’ll receive molded parts that meet your quoted design specifications for either new mold builds or major mold refurbishments.
- Major Mold Refurbishments: We can fix your ‘problem’ molds so they can produce parts that meet your specifications. We can also modify existing tooling to accomplish design changes that may occur after your product launch.
- Mold Cleaning, Service, and Maintenance: We perform scheduled maintenance on molds to ensure continuous optimal performance.
- Mold Transfers: We can quickly get your molds into production making quality parts whether you are moving them from another domestic plastics shop or is part of your reshoring process.
Engineered Resins
Engineered resins are specially formulated for parts that are subjected to demanding operating conditions. Some of the properties of engineered resins, versus commodity grade resins, include:
- Stronger Chemical Resistance.
- Exceptionally stable under high-temperature environments.
- Higher wear resistance
- Flame Retardant
- Increased impact resistance
- Higher tensile strengths
- Easy to machine
We carefully assess each job and select the engineered resin that best suits the specified operating environment. A sampling of the various engineered resins include:
- Nylon 6 (PA 6)
- Nylon 66 (PA 6-6)
- Nylon 12 (PA 12)
- Acrylonitrile Butadiene Styrene (ABS)
- Polycarbonate/Acrylonitrile Butadiene Styrene (PC/ABS)
- Cross Linked Polyethylene (PEX)
- Styrene Acrylonitrile (SAN)
- Thermoplastic Elastomer (TPE)
- Polybutylene Terephthalate (PBT)
- Polyoxymethylene - aka Acetel (POM)
- Polyphenylene Sulfide (PPS)
- Polyetheretherketone (PEEK)
- Polysulphone (PSU)
- Polyetherketones (PEK)
- Polyetherimide (PEI)
- Polyphenylene Ether (PPE)
Assembly Capabilities
Put it all together. As your full-service plastics manufacturer, we can decorate, assemble, and package your products to cut lead times, reduce costs, shorten the supply chain, and maintain quality throughout the production process. We can customize fully automated processes for your particular assembly, assemble it manually, or perform a hybrid of the two.
Some of the value-added assembly operations we offer include:
- Insert Molding
- Over molding
- EMI/RF shielding
- Insert heat staking
- Sonic welding
- Part decorating
- Pad printing
- Hot stamping
- Post-molding plastic painting
- Post-molding chrome plating
- Precision hand-manual assembly
- No defect leak detection
- Precision hole taping
- Custom packaging and kitting