The Ultimate Guide to Gas Assist Injection Molding
The Ultimate Guide to Gas Assist Injection Molding
By leveraging gas to perfect the molding process, manufacturers can now create lightweight, complex parts with superior strength and reduced waste. But how does it actually work? What advantages does it offer your operations? And where does the future of this technology lead?
Whether you’re a seasoned industry professional or looking to integrate Gas Assisted Injection molded parts into your production line, this ultimate guide covers everything you need to know.
What is Gas Assist Injection Molding?
Gas assist injection molding (GAIM) is an enhanced injection molding process often used for complex parts, large parts, and parts requiring an attractive, cosmetic finish.
The types of parts benefiting most from this process include:
- Large panels
- Enclosures
- Handles
- Doors
- Tube or rod-shaped parts
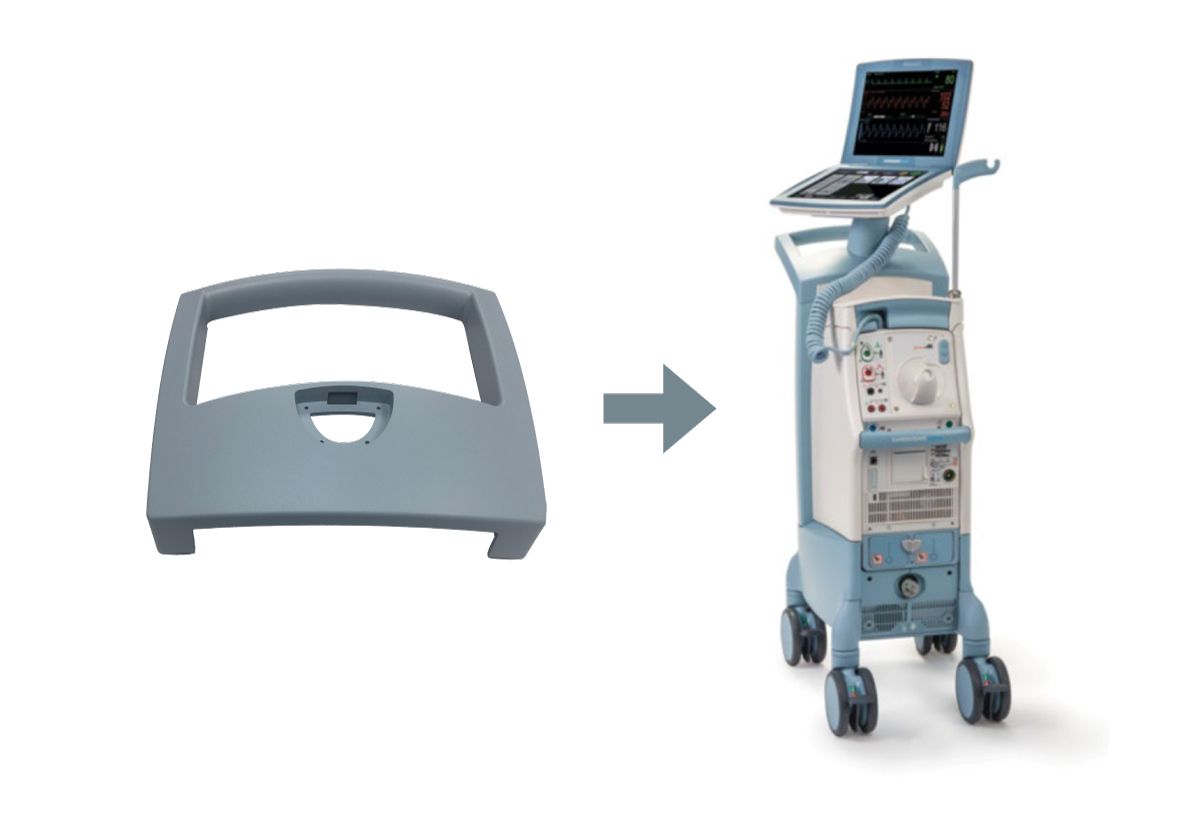
How Does Gas Assist Work?
The gas assist process is introduced at the end of the mold filling stage while the resin is still molten. Pressurized gas–usually nitrogen–is used in place of pack pressure from the molding machine. The pressure from the gas completes the filling of the mold cavity, forcing an even distribution of molten resin against the mold. The gas is held inside during the entire cooling phase and then is vented, leaving a hollow void. For internal gas-assist molding, the void is inside the plastic. For external gas assist molding, the void is on the outside surface, typically the backside of a part
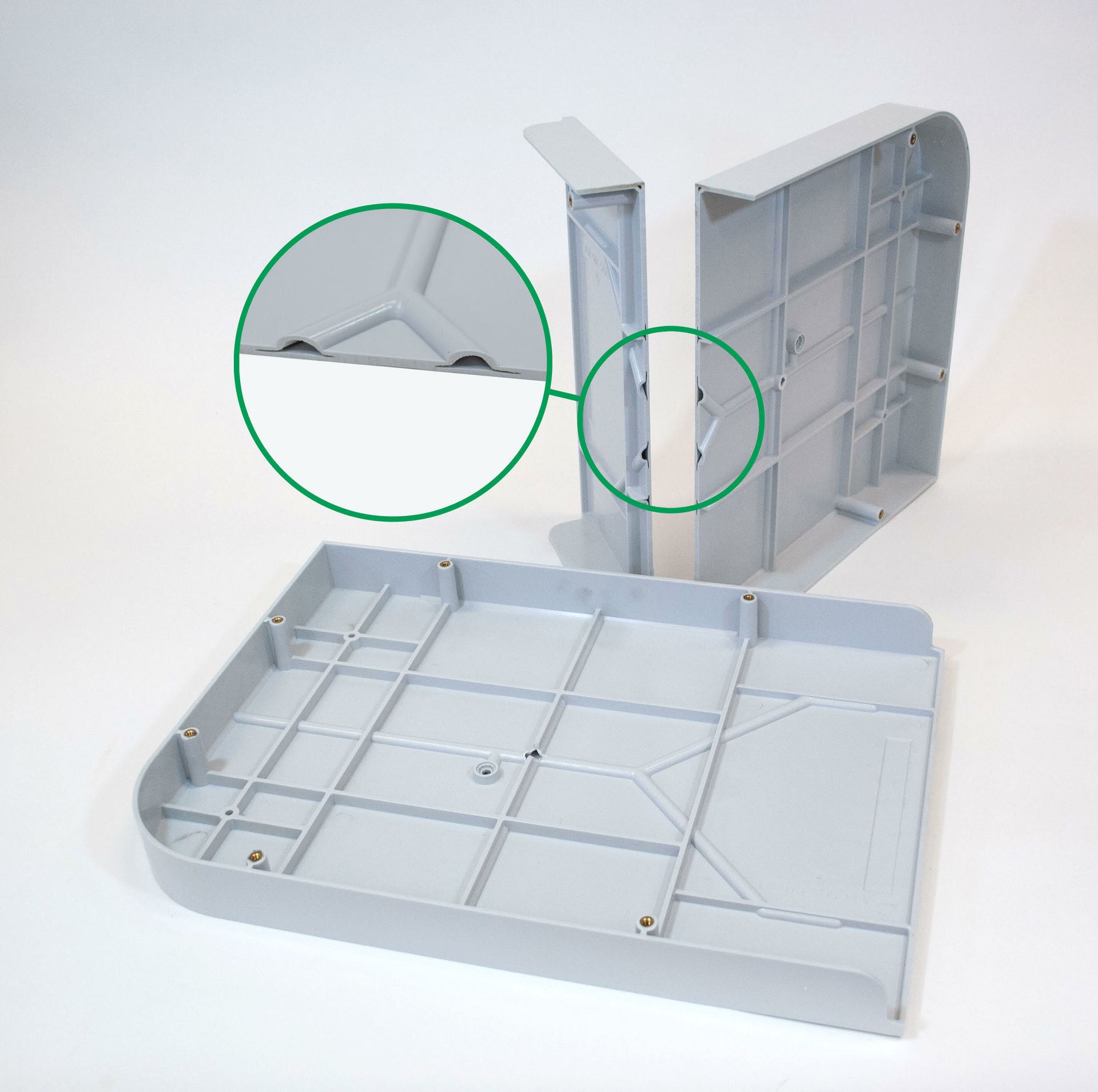
Benefits of Gas Assist
The gas-assist process gets results when part design elements make the part difficult to manufacture using straight injection molding. GAIM allows for more design flexibility while still being able to provide the following benefits:
- Higher stiffness-to-weight ratio in structural parts
- Reduced part weight
- Reduction of molded-in stress for improved dimensional stability
- Better surface finish
- Less part shrinkage
Design Advantages with Gas Assist
1. Complex Designs
For the design engineer, using GAIM expands design options and helps to minimize design changes to make the part manufacturable using injection molding. One of the greatest benefits is the ability to produce complex parts. Oftentimes with straight injection molding, parts having different wall thicknesses are molded separately and assembled later. GAIM allows multiple parts to be combined into one, reducing the need for secondary assembly processes–even if the parts have different wall thicknesses.
2. Large, Hollow Parts
The introduction of gas pressure aids in mold filling, providing uniform pressure throughout the part that lasts through the cooling stage. The result is a part with less shrinkage and reduced warpage. Part weight can also be reduced by creating hollowed out areas.
3. Cosmetic finishes
Where an attractive finished surface is required, gas-assist prevents sink areas that eliminate or at least minimize secondary operations to improve part appearance including sanding and priming.
Cost Benefits with Gas Assist
Gas assist injection molding offers several money saving benefits over traditional techniques, making it a go-to choice for many manufacturers today. Below we cover each one:
- Extended Tool Life — With gas-assist, lower clamping force is required because lower pressures are used. This results in less mold wear extending the life of the tool.
- Less Energy Cost — With lower clamping force required, larger molds can be used in smaller presses. Smaller presses consume less power and help to decrease the cost of manufacturing the part.
- Less Machine Time — A more rapid cooling period helps to reduce cycle time which in turn lowers manufacturing expense per part.
- Lower Material Cost — Less material is used to produce the part because hollow areas inside of the part are created with the gas and with less resin used, the part cost is lowered.
- Quality Results — With gas-assist injection molding, the process is typically easier to control than conventional injection molding. A dependable, repeatable process provides consistent production results and less waste.
Unlock the Power of Gas Assist Injection Molding with EnTech Plastics
Gas Assist Injection Molding is a powerful process that offers a range of advantages—from producing lightweight, complex parts to reducing waste and energy costs. Whether you're looking to improve your manufacturing process, reduce material usage, or enhance part quality, GAIM provides a flexible and cost-effective solution.
At EnTech Plastics, we specialize in delivering high-quality, custom injection molded parts tailored to your specific needs. If you're ready to explore how Gas Assist Injection Molding can optimize your operations, reach out to us today. Our team of experts is here to guide you through every step of the process and help you bring your next project to life.
Contact EnTech Plastics now to discuss your part manufacturing needs!
Be The First to Know!
Enjoying this article? Stay up to date and sign up now to get notified of new news and insights from EnTech Plastics.