Overmolding and Insert Molding: Enhancing Product Functionality
In the world of plastic injection molding, achieving complex and multifunctional product designs often requires innovative techniques. Two such techniques, overmolding and insert molding, have gained prominence for their ability to enhance product functionality and versatility.
In this blog, we will explore the concepts of overmolding and insert molding, understand their differences, delve into their applications, and examine the advantages they bring to the world of manufacturing.
Understanding Overmolding and Insert Molding
Overmolding and insert molding are specialized injection molding processes that involve combining multiple materials or components to create a single product. These techniques are employed to add a layer of material or incorporate separate components into a primary molded piece. While they share some similarities, they have distinct applications and use cases.
Overmolding:
Overmolding is a process where a second material is molded over a pre-existing part or substrate. The primary part (the substrate) is typically made of a rigid material, while the overmold material is often elastomeric or soft, creating a soft-touch or ergonomic grip.
Overmolding is commonly used to enhance product aesthetics, ergonomics, and grip comfort. It also provides durability and protection to the underlying component.
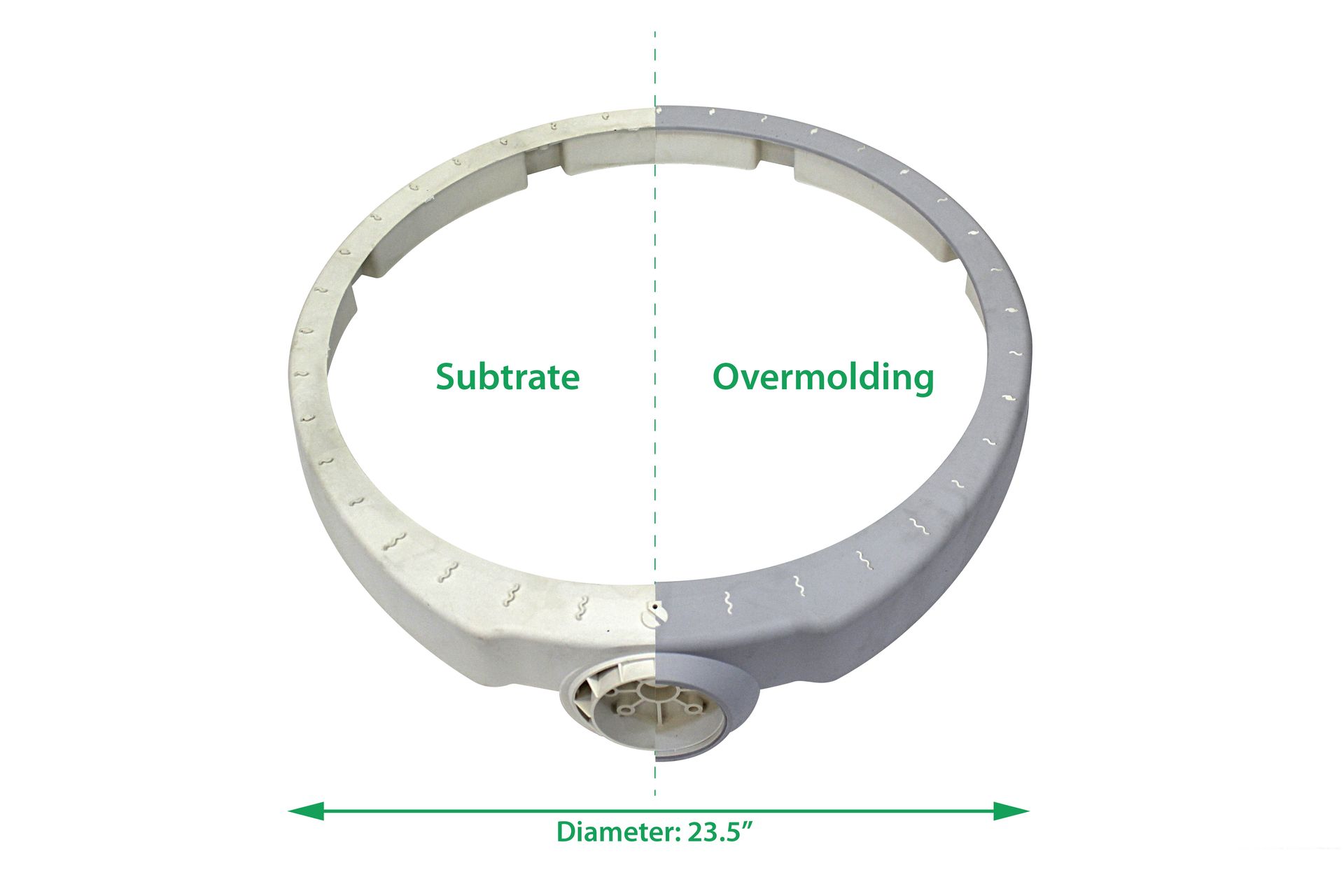
Insert Molding:
Insert molding, on the other hand, involves molding a pre-manufactured component (the insert) into a cavity within the primary part. The insert can be made of various materials, such as metal, plastic, or even electronics.
Insert molding is employed when functionality is required from the inserted component, such as electrical conductivity, reinforcement, or attachment points.
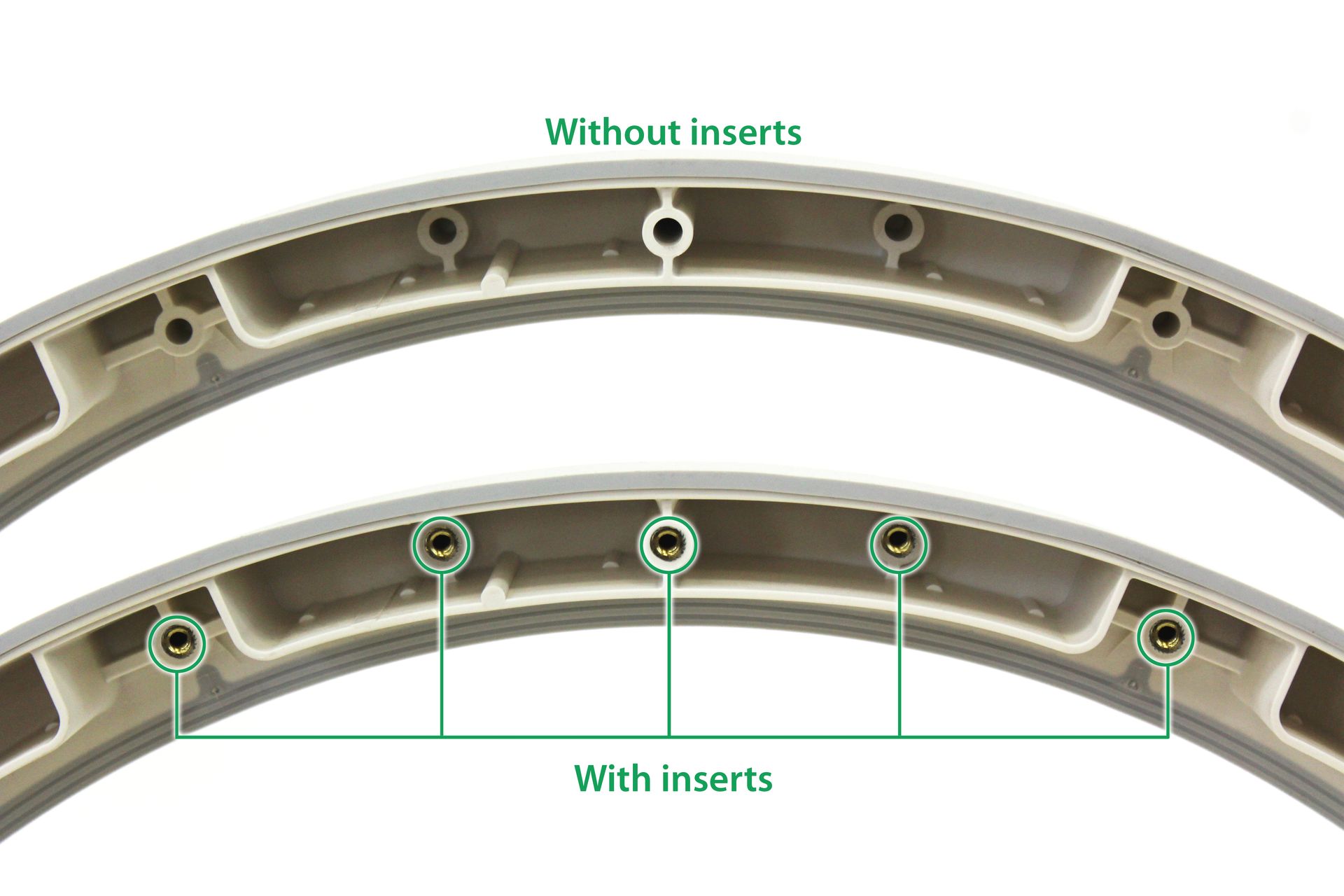
Applications of Each
Overmolding
Overmolding offers a wide range of applications across various industries. Here are some common examples:
- Consumer Electronics: Overmolding is used to create ergonomic grips on tools, remote controls, and devices like toothbrushes. It also provides shock resistance for delicate electronic components.
- Medical Devices: Overmolding is used to create comfortable, non-slip handles for surgical instruments. It also provides sealing and insulation in medical device components.
- Sporting Goods: Handles and grips for sports equipment like bicycle handles, golf club grips, and fishing rod handles are frequently made using overmolding.
- Toys and Games: Overmolding adds safety features to toys and games, such as soft edges on hard plastic parts to prevent injuries.
Insert Molding
Insert molding has diverse applications across several industries due to its ability to integrate various materials and components:
- Medical Devices: Insert molding is crucial for medical devices that require precise positioning of metal components like needles or electrodes within plastic parts or to encapsulate metal components like inserts for threaded fasteners or electrical connectors. It enhances structural integrity and reduces assembly steps.
- Electronics: In electronics manufacturing, insert molding is used to embed connectors, switches, and sensors directly into plastic housings. This process ensures a secure connection and protects sensitive electronics from external factors.
- Aerospace: Components with stringent weight requirements often use insert molding to combine lightweight plastics with metal reinforcement for critical parts.
- Appliances: Many household appliances use insert molding for electrical connectors, sockets, and control interfaces, ensuring reliable performance and ease of assembly.
Advantages of Overmolding and Insert Molding
Overmolding and insert molding offer numerous advantages that enhance both product performance and manufacturing efficiency. By incorporating multiple materials or components, these techniques improve product functionality while adding new features or reinforcing existing ones. They also contribute to cost savings by eliminating secondary assembly steps, streamlining production, and reducing labor costs.
Additionally, overmolding enhances product aesthetics by introducing color contrasts or soft-touch surfaces, while insert molding ensures clean, integrated designs. These processes also help minimize material waste, using only what is necessary to achieve the desired functionality. Furthermore, by encapsulating or reinforcing components, both techniques enhance product durability, ensuring longevity and reliability. Designers also benefit from increased flexibility, allowing them to create innovative and visually appealing products with unique features.
Challenges and Considerations
While overmolding and insert molding offer numerous benefits, they also present some challenges and considerations:
- Material Compatibility: Ensuring that the primary and overmolded/inserted materials are compatible is crucial to avoid bonding issues or material degradation.
- Tooling Complexity: These processes may require more complex molds and tooling, which can increase initial setup costs.
- Tolerance Control: Maintaining precise tolerances can be challenging when combining different materials. Close collaboration between designers and manufacturers is essential.
- Assembly and Insertion: In insert molding, the accurate placement of inserts is critical to achieve proper functionality.
- Production Speed: Overmolding and insert molding may have longer cycle times compared to conventional injection molding due to additional steps.
Enhance Your Products with Advanced Injection Molding Techniques
Overmolding and insert molding are invaluable techniques in the world of plastic injection molding, offering a myriad of possibilities to enhance product functionality, aesthetics, and versatility. Whether you seek to create ergonomic grips, reinforce components, or integrate electronics into your products, these processes open doors to innovative designs and cost-effective manufacturing solutions. Understanding their applications, advantages, and considerations is essential for successful product development and manufacturing.
At Entech Plastics, we specialize in precision overmolding and insert molding solutions tailored to your unique needs. Whether you're developing a new product or optimizing an existing design, our expert team is here to help.
Contact us today to learn how we can bring your ideas to life with cutting-edge injection molding technology!
Be The First to Know!
Enjoying this article? Stay up to date and sign up now to get notified of new news and insights from EnTech Plastics.