Understanding Tolerances in Custom Injection Molding
Custom injection molding is a versatile manufacturing process widely used for producing a vast range of plastic parts and components. One critical aspect that manufacturers and designers must grasp to ensure successful injection molding projects is tolerance. In this blog, we delve into the world of tolerances in custom injection molding; exploring what they are, why they matter, and how to manage them effectively for high-quality results.
What Are Tolerances in Injection Molding?
Tolerances in injection molding are the allowable limits for variations in the dimensions, geometry, and features of a molded part. These limits are specified to ensure that the final part meets the design requirements and functions correctly. Tolerances are expressed as a range of acceptable values around a nominal dimension or feature. They are crucial because they help define the part's quality, functionality, and compatibility with other components in an assembly.
Why Do Tolerances Matter?
Maintaining precise tolerances helps guarantee consistent quality across production runs. When every part performs reliably, you reduce the risk of costly rework, warranty claims, or functional failures. Tolerances also have a direct impact on assembly. When different components come together—whether it’s a snap-fit housing or a sealed enclosure—accurate tolerances ensure compatibility and performance.
However, it’s not always about going as tight as possible. Tight tolerances require more sophisticated tooling and stringent process controls, which can drive up costs. In contrast, looser tolerances may lower production expenses but can compromise fit and function. Striking the right balance is key.
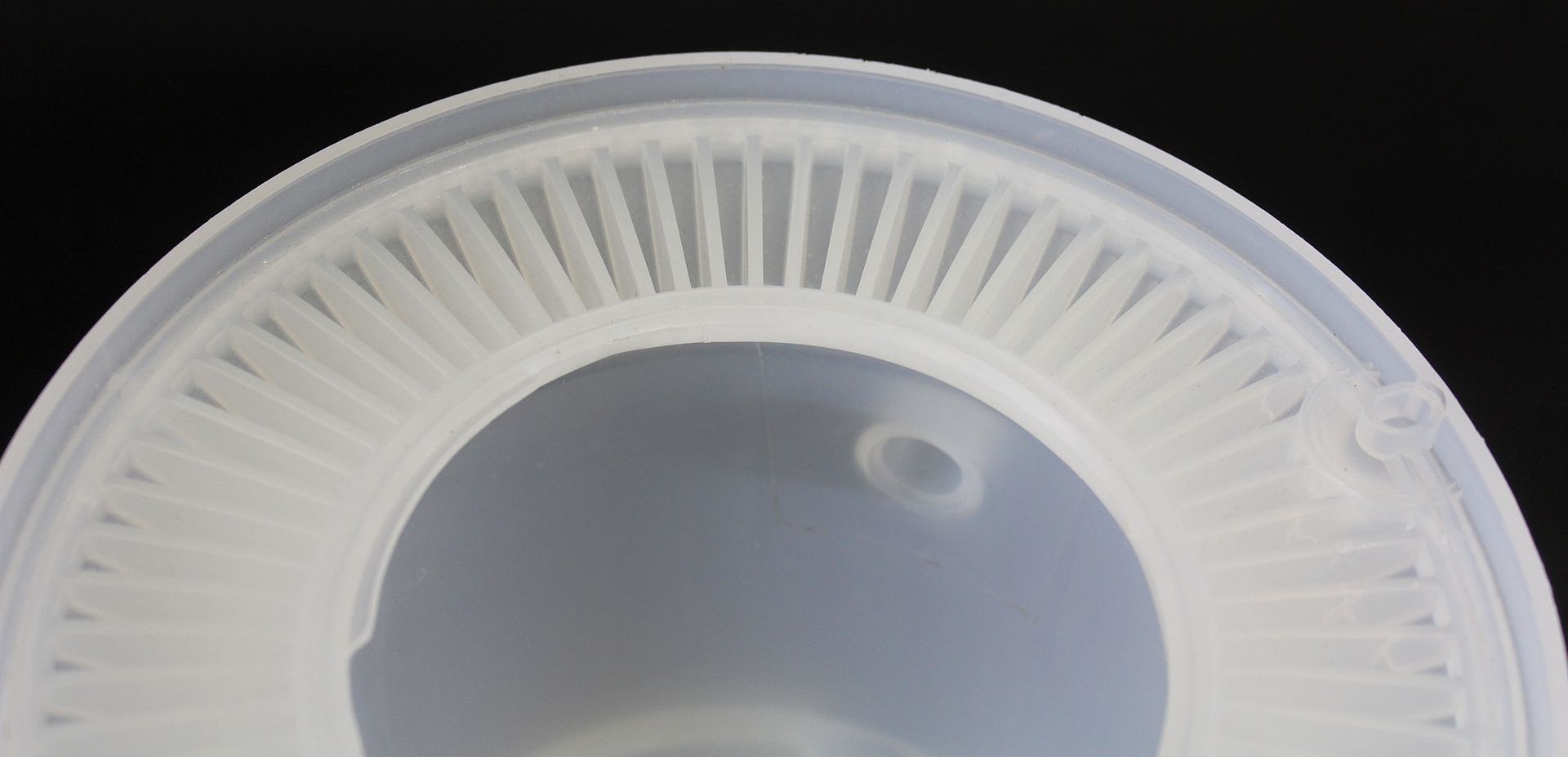
Types of Tolerances in Injection Molding
In injection molding, you'll encounter two main types of tolerances:
- Dimensional Tolerances:
These tolerances relate to the size and shape of the part, including features such as length, width, and height. For example, a part with a specified length of 100 mm and a tolerance of ±0.1 mm means that the acceptable range for the length is 99.9 mm to 100.1 mm.
- Geometric Tolerances: Geometric tolerances involve more complex aspects of the part's geometry, such as the flatness of a surface, the perpendicularity of features, or the concentricity of holes. These tolerances specify the allowable deviation from the ideal geometric condition.
Factors Affecting Tolerances in Injection Molding
Several factors can influence the tolerances achievable in custom injection molding:
- Material Properties:
Different thermoplastic materials have varying levels of shrinkage and thermal expansion, affecting how they conform to the mold. High-performance engineering plastics can provide tighter tolerances.
- Tooling and Mold Design:
The precision of the mold design and tooling is crucial. High-quality molds and tooling allow for tighter tolerances.
- Process Control:
The injection molding process must be tightly controlled to maintain consistency. Factors like temperature, pressure, and injection speed can impact part dimensions.
- Part Design:
The part's design itself plays a significant role. Features like wall thickness, draft angles, and the location of gates and ejector pins can affect how well tolerances can be maintained.
Balancing Tolerance and Cost
While it’s tempting to aim for the tightest possible tolerances across the board, this isn’t always practical—or necessary. Pushing for ultra-precise tolerances may dramatically increase production costs without offering real value. That’s why it’s important to work with your injection molding partner to determine where tight tolerances truly matter, and where there’s room for flexibility.
Often, this balance is achieved through close collaboration between designers, engineers, and molding professionals. The goal is always to meet functional requirements without overengineering the part or overextending the budget.
Communicating Tolerance Requirements
Clear communication is everything. That starts with detailed technical drawings that specify which dimensions are critical, along with any necessary geometric tolerances. Using standard symbols and best practices—such as GD&T (Geometric Dimensioning and Tolerancing)—helps ensure everyone is on the same page. It’s also a good idea to consult with your molding partner early in the design phase. At EnTech Plastics, we work closely with customers to review tolerance needs and recommend achievable solutions that won’t inflate production costs or compromise performance.
Design with Tolerance in Mind
Tolerances are more than just numbers on a spec sheet—they’re a key part of how your product performs, fits, and functions. By understanding the different types of tolerances, what affects them, and how to manage them effectively, manufacturers can create injection-molded parts that meet both quality standards and production goals.
If you're developing a new product or refining an existing one,
reach out to the team at EnTech Plastics. We'll help you design with the right tolerances in mind, ensuring your project runs smoothly from concept to completion.
Be The First to Know!
Enjoying this article? Stay up to date and sign up now to get notified of new news and insights from EnTech Plastics.